9 Lessons to Get ‘Right’ Integrator
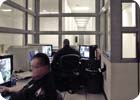
When it comes time to integrate security at your enterprise, it’s vital to get the right integrator for the job.
Choosing the wrong integrator can have costly repercussions, from poor installation to expensive change orders. An integrator whose business model focuses on your type of business or government facility will usually provide a higher quality installation, including tighter security.
The following nine no-nonsense rules will help you select the best security integrator for your facility.
1. Integrator Pre-qualification
Systems integrators work in multiple industries, from manufacturing to water treatment to retail security. Security system integrators also specialize in various sub-fields. Still, because systems vary depending on facility type, integrators often cross “disciplines” to work on a variety of project types.
Many facilities present challenges that the average facility does not. An integrator may need to incorporate systems such as security video, access control, perimeter detection, personal alarm and duress, video visitation, guard tour and many others. An integrator, who understands not only the “black boxes,” but also your specific facility, is invaluable.
Thus, systems integrators should be pre-qualified to bid on work at your type of business or facility. An “open” specification is a mistake because it allows anyone who has installed a camera or access control system to provide the full integration. Hiring a vendor with a lack of experience often results in delays and even disastrous outcomes. Listing several integrators with proven track records is a good start to limiting exposure.
2. Due Diligence in Contractor Selection
You wouldn’t hire staff without checking references; the same applies to security integrators. On traditional design projects, an owner’s design team should follow up on proposed integrators’ references. In some cases, RFPs for services are listed without a design professional’s assistance.
Things to look for include past performance; other facilities’ experiences with specific integrators; and, depending on the facility’s type and size, its design documents should establish a baseline for integrator experience.
3. Proprietary vs. Non-Proprietary Systems
Product manufacturers, designers and integrators have argued over the definition of “proprietary” for many years. When considering facility systems, it’s important to consider the term as it applies to the products that are used within the facility. In a general sense, products that are available only from a single source, aren’t installed or maintained by several integrators or cannot be purchased from multiple vendors fall into the “proprietary” category.
Allowing a contractor to install proprietary products can cost in the future, even if it dramatically saves at first. First, it’s likely that a limited number of integrators can work with a proprietary product. This can complicate future bidding processes. More importantly, a proprietary product’s manufacturer, and only that company, provides upgrades and maintenance. If that company goes out of business, their products -- and the support for it -- are no longer available. While a smaller operation with a good product and even a large installed client base can be attractive, larger and better-known companies are less likely to disappear.
It may seem forward thinking to opt for the latest and greatest product out there. It’s wiser, however, to specify a product with a good track record and a promise of future savings.
4. Require Factory Acceptance Testing
To ensure that your desired system works the way you expect, the integrator must test it against the design documents. This testing ensures that the head-end equipment has been wired and programmed correctly. Then, once the equipment is delivered to the site, troubleshooting is limited to the field devices and terminations of wire and cable.
The integrator should provide a written plan listing all devices and tests. The testing, conducted off-site, should include simulations of all field device inputs and outputs. The integrator should also test all subsystems to be included in the final projec
5. Add the Raceway or Future Installations
One challenge in construction such as correctional facilities and some other hardened buildings is routing conduit, which will be concealed in a facility made entirely of poured-in-place concrete, concrete block walls and grout-filled concrete block walls. Conduit work requires close coordination between the electrical and structural engineering contractors. Without such coordination, facility owners face the expensive task of cutting block and concrete to conceal a missed conduit, or add a camera, intercom, or other device after construction.
6. Owner Involvement
Having experienced designers and integrators is important. However, the owner’s full, early involvement with this team is crucial to success. Operational policy and procedures, the number of staff available and how this organization is run can change your security system’s overall layout, including both physical and electronic designs. Moreover, not only managers should provide input--operational staff opinions are critical, too.
7. Have Realistic Expectations
Knowing the integrator’s delivery and final product terms must come early in the process. Otherwise, a facility owner can become overwhelmed by a complex project’s integration, especially because the other trades must complete much of their work prior to the integrator introducing sensitive electronics. Developing project milestones and ensuring adequate tracking is key to limiting end-of-project surprises.
8. Follow Up on Post Construction Responsibilities
Often, once the project is finished, end-users take ownership, move on and continue business as usual. It’s important that the systems integrator provide all required closeout documentation. This includes as-built drawings, equipment owners’ and maintenance manuals and other facility-specific schedules and manuals. These important documents should be stored in a location that’s readily accessible to management and maintenance staff for future upgrades or renovations.
9. Do Your Homework
Many resources exist to help an end user understand the systems integrator selection process. Architectural/engineering firms and consultants involved in your specific industry are one key resource. Often, an already-employed firm already has someone on staff to assist this process. The reason for using a specially trained security integrator is two-fold: They will save you both time and money, and their specialty will provide tighter security and smoother operations – thereby getting it “more” right -- in the long run. v
Looking for a reprint of this article?
From high-res PDFs to custom plaques, order your copy today!