Good Looks and Security, Too
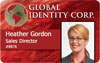
Brand awareness is an important aspect for some enterprises. Holographics can also add higher security. Photos courtesy of ID Wholesaler
Before the advances in card and badge printers and the sophisticated software that goes with them, many security operations went to outside print houses. The service would design the card, print the cards and ship them back to the customer.
Today, most organizations design and print themselves.
At the same time, there needs to be more concentration on the card and badge design. There are many elements involved.
Today, most organizations design and print themselves.
At the same time, there needs to be more concentration on the card and badge design. There are many elements involved.
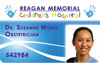
ID CARD DESIGN TIPS
Consider the use of your cards and the level of security you need. Knowing whether you’ll need to use holographic laminates or cards with embedded security features is important as you begin designing your cards. Custom holographics can include designs and logos to extend your brand identity in the form of foils or laminates.
Consider the type of cards you’ll be printing on. You may need to design your card around an embedded security feature, smartcard contact chip, a magnetic stripe or barcode. If you’re using a reverse transfer printer, take advantage of its print quality by using colorful imagery.
How much printed information will your cards contain? Make a list of the data specifications your cards will need so you’re sure to include all necessary elements in your design. Consider printing information not necessary for visual ID on the back of the card. This will also keep the front of your card uncluttered, easier to read, and more professional looking.
Consider the type of cards you’ll be printing on. You may need to design your card around an embedded security feature, smartcard contact chip, a magnetic stripe or barcode. If you’re using a reverse transfer printer, take advantage of its print quality by using colorful imagery.
How much printed information will your cards contain? Make a list of the data specifications your cards will need so you’re sure to include all necessary elements in your design. Consider printing information not necessary for visual ID on the back of the card. This will also keep the front of your card uncluttered, easier to read, and more professional looking.
ORIENTATION AND USE
Determine the orientation of your cards. Considerations: How will the cards typically be used or displayed – if they’ll require a hole punch so the cards can be worn on a clip or lanyard, you’ll want to design around the area the slot will be punched. Orientation of your organization’s logo – if it’s longer, it may require using a horizontal layout so that your logo is clearly legible. The size of the text fields you’ll need – horizontal layouts can allow for longer fields.
Graphic design is important. A well-designed card will support and extend your brand, representing your brand not only to your cardholders, but also to visitors and anyone else who sees them. In addition, how many times have you seen people wearing ID cards while out to lunch or running errands?
Bright, saturated color looks best printed on PVC cards. Light colors tend to look faded or washed out. Also be careful of the amount of dark color used. Consider using a custom or stock image, illustration or other design or texture as a background -- make sure to use high resolution, print quality images (300 dpi). Stock imagery is easily available online at a reasonable price and can take cards from looking elementary to looking professional.
Graphic design is important. A well-designed card will support and extend your brand, representing your brand not only to your cardholders, but also to visitors and anyone else who sees them. In addition, how many times have you seen people wearing ID cards while out to lunch or running errands?
Bright, saturated color looks best printed on PVC cards. Light colors tend to look faded or washed out. Also be careful of the amount of dark color used. Consider using a custom or stock image, illustration or other design or texture as a background -- make sure to use high resolution, print quality images (300 dpi). Stock imagery is easily available online at a reasonable price and can take cards from looking elementary to looking professional.
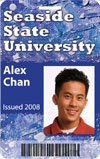
PEOPLE PHOTOS
What about the cardholder’s photo? Photos taken against a white background look best – consider purchasing an inexpensive photo backdrop. There are drivers available that make automatic face recognition, cropping, image enhancement and image acquisition easy within your photo ID software application. Make sure the images are high resolution.
Print quality counts. Reverse-transfer printing technology provides the best print quality available in card printing. Reverse transfer printers provide photo-quality printing and, unlike printers using direct-to-card printing technology, they are capable of printing on the entire surface of cards. Direct-to-card printers aren’t capable of printing right up to the edges of cards. They can leave a small but noticeable unprinted border around the entire card. Reverse-transfer printers are even capable of high-quality printing on technology cards, like proximity cards with internal antennas that make the surface of the card uneven and difficult for direct-to-card printers to print on. They can also print right up to the edges of the exposed chip on a contact smart card.
Test the printing for quality. You’ll never know exactly what your cards will look like until you test print them on your card printer. Dye sub printing on PVC outputs color differently than printing on paper with an inkjet printer. Your printer drivers will allow you to make adjustments that will affect the print outcome—adjusting settings can change the intensity of color on your cards, for example.
Print quality counts. Reverse-transfer printing technology provides the best print quality available in card printing. Reverse transfer printers provide photo-quality printing and, unlike printers using direct-to-card printing technology, they are capable of printing on the entire surface of cards. Direct-to-card printers aren’t capable of printing right up to the edges of cards. They can leave a small but noticeable unprinted border around the entire card. Reverse-transfer printers are even capable of high-quality printing on technology cards, like proximity cards with internal antennas that make the surface of the card uneven and difficult for direct-to-card printers to print on. They can also print right up to the edges of the exposed chip on a contact smart card.
Test the printing for quality. You’ll never know exactly what your cards will look like until you test print them on your card printer. Dye sub printing on PVC outputs color differently than printing on paper with an inkjet printer. Your printer drivers will allow you to make adjustments that will affect the print outcome—adjusting settings can change the intensity of color on your cards, for example.
UNDERSTAND PRINTER CHOICES
Before you purchase a printer, design a card and start production, there are a few things you should know about the printers. The type of printer you choose will depend largely on the type of card you plan to use, how many cards you plan to print, how often you need to print cards and what printing elements you need to incorporate into your card. There are five major factors to consider.CARD SIZE
Most driver’s licenses and other “hard cards” found in wallets and purses have the same physical dimensions. This is the standard CR-80 card, measuring about 3.375 x 2.125 inches (85.5mm x 54mm) and 30 mil (0.75mm) thick.
PRINTING SPEEDS
Card printers come with a variety of card printing speeds. Some simply print faster than others while others speed printing by printing both sides of the card, while others print only one side of a card. In general, the faster cards are printed, the more expensive the printer. In some situations, cards need to be printed immediately while other cards can wait to be printed. This is typically called on-the-spot or on-premise printing.
THE PHYSICAL PROPERTIES OF THE PRINTER
If you are working in an office that’s short on space, you’ll want a printer with a small footprint. If other work must be accomplished while the printer is printing, you will also want to make sure you purchase a printer that’s on the quiet side. While the size and loudness of a printer may not be a concern in a factory, it is very important in an application such as a cruise ship.
EASE OF USE
A card printer should be easy to use, right out of the box, especially if the people using it are not overly familiar with printers.
THE TYPE OF PRINTING
This includes thermal, dye sublimation, or mass transfer printing.
Thermal printing -- Like all other desktop printers in the office, today’s photo ID printers are digital. In the years since the first dot matrix printers arrived on the scene, we’ve become used to text and images composed of tiny dots - picture elements or pixels. Early results were not impressive, due to the print head’s then-limited resolution, measured in dots per inch or dpi. With today’s resolutions, the problem of jagged edges is largely a thing of the past.
Most photo IDs are printed by digital thermal transfer, a process by which color is transferred from a single-use ribbon to various kinds of receptor materials. There are two distinctly different thermal transfer technologies: dye sublimation, using the three process colors yellow/magenta/cyan for photo-realistic images, and mass transfer, for machine readable text and barcodes (usually in black). Both technologies use a stationary print head comprising a row of closely spaced resistive elements — tiny heaters, independently energized by the printer controller. Sandwiched by spring pressure between the print head and the receptor is the inking ribbon, which may be either a resin-coated film for mass transfer, or a series of process-color dye panels for dye sublimation.
The receptor card is driven through the print station, with the ribbon metered out at the same speed from the supply roll.
Dye sublimation printing – The variable size and density of each color dot is the secret to the photo-quality printing possible with dye sublimation – bright colors and no jagged edges. Dyes penetrate the receptor. Color migrates from the dye ribbon into the surface. The spread of the dye dot (its amount of diffusion) depends on the amount of heat applied by the printhead element. On reaching a dye panel boundary, the printhead is lifted to allow the card to back up. The head then lowers to print the next color.
Mass transfer printing -- With a mass transfer panel, the printer cannot control either the ink dot’s size or density. It’s either there or it isn’t, which is not good for continuous tone images such as photographs. To create the illusion of continuous tone from discrete dots of ink, printers use a process called dithering, exactly the same behind-the-scenes operation your computer performs anytime it sends a picture to the office laser printer.
A mass transfer ribbon is a layer of monochrome resin, usually black, on a thin backing film (also called black resin printing). When heated, the resin is stripped from the backing and deposited as a physical layer on the receptor. Mass transfer delivers sharp text and graphics plus infrared readable barcodes. Photo reproduction is adequate for many applications calling for high printing speed and low cost.
Understanding the basic elements of a high-quality ID card and the fundamentals of the printing process, security executives can better choose the right printer for the specific application.
Thermal printing -- Like all other desktop printers in the office, today’s photo ID printers are digital. In the years since the first dot matrix printers arrived on the scene, we’ve become used to text and images composed of tiny dots - picture elements or pixels. Early results were not impressive, due to the print head’s then-limited resolution, measured in dots per inch or dpi. With today’s resolutions, the problem of jagged edges is largely a thing of the past.
Most photo IDs are printed by digital thermal transfer, a process by which color is transferred from a single-use ribbon to various kinds of receptor materials. There are two distinctly different thermal transfer technologies: dye sublimation, using the three process colors yellow/magenta/cyan for photo-realistic images, and mass transfer, for machine readable text and barcodes (usually in black). Both technologies use a stationary print head comprising a row of closely spaced resistive elements — tiny heaters, independently energized by the printer controller. Sandwiched by spring pressure between the print head and the receptor is the inking ribbon, which may be either a resin-coated film for mass transfer, or a series of process-color dye panels for dye sublimation.
The receptor card is driven through the print station, with the ribbon metered out at the same speed from the supply roll.
Dye sublimation printing – The variable size and density of each color dot is the secret to the photo-quality printing possible with dye sublimation – bright colors and no jagged edges. Dyes penetrate the receptor. Color migrates from the dye ribbon into the surface. The spread of the dye dot (its amount of diffusion) depends on the amount of heat applied by the printhead element. On reaching a dye panel boundary, the printhead is lifted to allow the card to back up. The head then lowers to print the next color.
Mass transfer printing -- With a mass transfer panel, the printer cannot control either the ink dot’s size or density. It’s either there or it isn’t, which is not good for continuous tone images such as photographs. To create the illusion of continuous tone from discrete dots of ink, printers use a process called dithering, exactly the same behind-the-scenes operation your computer performs anytime it sends a picture to the office laser printer.
A mass transfer ribbon is a layer of monochrome resin, usually black, on a thin backing film (also called black resin printing). When heated, the resin is stripped from the backing and deposited as a physical layer on the receptor. Mass transfer delivers sharp text and graphics plus infrared readable barcodes. Photo reproduction is adequate for many applications calling for high printing speed and low cost.
Understanding the basic elements of a high-quality ID card and the fundamentals of the printing process, security executives can better choose the right printer for the specific application.
Looking for a reprint of this article?
From high-res PDFs to custom plaques, order your copy today!