The Science of Safety
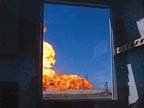
The road to building safety has been beset by a series of terrorist bumps in recent years, but fortunately new, scientifically engineered practices and materials are emerging to pave the way toward reliable workplace security.
It may come as a surprise that the catalyst for the nation’s recent prioritizing of building safety was not the Sept. 11 terrorist attacks, but rather the 1995 bombing of the Alfred P. Murrah Building in Oklahoma City. That rather singular incident of domestic terrorism sparked a widespread change in the way the federal government analyzes building security safety measures.
Of course, September 11, 2001 also has had a profound impact on worldwide safety measures. According to Carol Borow, president of CHB Industries, one of the nation’s largest providers of security film for government and commercial facilities, the devastating attacks awakened the private sector to safety risks. “In recent years, corporate building owners have become increasingly blast conscious. They are now aware that specialized materials, such as safety glass films, can help mitigate damage caused by attack or natural disaster.”
The war and ongoing rebuilding efforts in Iraq have also sustained demand for safety films and related systems. Barker noted that his firm has seen the greatest increase in private sector demand coming from financial institutions, chemical manufacturers and telecommunications providers. Yet while commercial property managers may have become more educated on safety measures recently, they still lag behind the government in one critical area: testing.
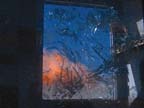
protection can create more human damage.
Replicating the unthinkable
After years of ad hoc testing that varied from project to project, the General Services Administration (GSA) established a test protocol and published criteria requiring specific performance levels for federal approval. While the GSA standards remain active for government buildings, the private sector has not followed with its own commercial performance standards for blast-resistant glass film systems. Some experts fear the lack of universal standards could potentially create a ‘wild west’ syndrome, particularly given certain limitations of the GSA standard.“Even the GSA hasn’t required films to pass for multiple test samples – only a single pass is required,” said Borow. “When dealing with something as critical as human lives, it’s necessary to present clients with reliable, ‘plottable’ data rather than cherry-pick the most favorable results.” Despite this deficiency, Borrow maintains the GSA standards have merit because they compel manufacturers to invest in testing as well as research and development.
Barker agrees that test results can often be a gray area. “For some buildings, installing a safety film can actually increase the risk of structural damage,” he cautions. “It is always advisable to have an unbiased third party conduct an engineering-driven analysis of the property’s needs before selecting any safety system.”
Experts recommend that property owners conduct a security vulnerability assessment to calculate a building’s risk potential and design a customized risk-reduction solution. A thorough assessment consists of a physical security inspection, explosion threat definition, computer modeling to determine blast loads, structural analysis to gauge potential collapse, and even estimated loss-of-life projections based on various scenarios. Federal anti-terrorism experts estimate that upwards of 70 percent of injuries in a building blast scenario are lacerations resulting from glass shrapnel, making windows a significant focal point in the analysis.
Such an assessment can be time consuming and expensive, but it is imperative for matching risk mitigation techniques to a particular building’s needs. Responsible film manufacturers and installers will absorb the cost of the evaluation – even if it means glass films are not included in the final specification – to ensure that their client receives a reliable solution that will perform consistently with expectations.
Whether required by the GSA for certification or not, responsible glass film manufacturers conduct an array of tests designed to simulate real world trauma, such as impact, puncture, tear, wind, weather, burn and ignition. The impact test consists of dropping steel balls ranging from five to 100 pounds on filmed glass from a variety of heights. Wind tests require the use of vacuum cycling machines that assess how shattered glass will respond to violent winds. To simulate weather, manufacturers place filmed glass in xenon and moisture chambers to gauge the affects of harsh weather on adhesion. Scientists also direct a flamethrower at the material to measure its ability to withstand fire without generating noxious smoke.
But most dramatic are the blast assessment and burn tests. In this test, a manufacturer contracts with independent labs to detonate high explosives, examining the product’s ability to absorb blast energy and reduce damage and injury. Carl Kernander, a technical manager for Madico (Woburn, Mass.) highlighted a rarely mentioned test element. “During a blast, windows must absorb two separate loads. First, a positive load applies inward force on the glass, then the detonation creates a vacuum that generates a negative pressure load on the glass.” Kernander explained that the desired function of the film is not to prevent the window from shattering, but rather to bind the shards together, preventing either load from releasing deadly shards onto the street or into the building.
Of course, there is more to comprehensive building security than glass safety. “Perimeter security,” said Barker, “is increasingly used to reduce risks. Moving the protected perimeter away from a building can dramatically reduce the blast loads on the structure.”
Perimeter security is typically deployed to protect structures from external attacks, such as car bombs, or short-range strikes like the recent attack on the Sheraton Baghdad. However, traditional blockades such as Jersey barriers and steel pylons have fallen into disfavor because they can negatively impact aesthetics and employee productivity. Bobby Hahn, a technical sales specialist in Madico’s safety film group, explained, “Employees in high profile buildings are sufficiently aware of global affairs. They do not want to be reminded of the risks they face on a daily basis.”
One way buildings are improving security without alarming employees is by installing more natural exterior barriers. Many commercial complexes have positioned large concrete planters along the border of the building and some have even placed hefty rocks in front of high risk areas. These techniques provide the same basic function as would a Jersey barrier, but do so more discretely, without disrupting the delicate balance between security and comfort levels.

safely absorb the impact of a blast
Natural threats dominate
Although Madico estimates that demand for blast-resistant safety films has increased from 30 percent of sales to nearly 70 percent since Sept. 11, building owners in certain parts of the world are seeking protection against other types of disasters, particularly earthquakes and storms.Ultimately, regardless of whether a threat is man-made or naturally occurring, pioneering companies are testing the limits of science to provide government and commercial building owners with materials and equipment designed to reduce risk. It’s a realization that has been painfully driven home by the terrorist bump; buildings may never be immune to attack or storm, but they can be better prepared.
Looking for a reprint of this article?
From high-res PDFs to custom plaques, order your copy today!