Pittsburgh International Airport Spreads Its Wings
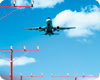
Accommodating almost 10 million travelers each year, Pittsburgh International Airport (PIT) has been recognized by organizations including J.D. Power and Associates for its high quality in meeting travelers’ needs. With new routes being added each year and development surrounding the airfield growing, the airport is a major economic engine for southwestern Pennsylvania. And, of course, fire alarm systems are needed to ensure that should a fire or event occur, all occupants could be alerted of such an event.
“We needed a larger terminal with modern jet ways not only for the growing number of flights, but also for the larger aircraft passing through the airport,” said Tom Long, director of maintenance and a 38-year PIT employee. “We also knew the original facility contained asbestos, as well as old building control equipment that were not able to be upgraded.”
FIRE SAFETY APPLIED
Construction on the new Pittsburgh International Airport began in 1990, designed to offer 7.7 million square feet of air-side space, more than 100 gates, and a mall of more than 100 restaurants and specialty shops. Based on the company’s more-than-40-year relationship with the airport, PIT and its architectural consultants tapped Honeywell to supply heating, ventilation and air conditioning (HVAC), and fire alarm systems throughout the new space.To assist in managing this wide array of equipment, two full-time Honeywell technicians work with the airport’s maintenance department as part of an ongoing service agreement, maintaining equipment and supervising much of the fieldwork.
“It’s an integrated team,” Long said. “Honeywell takes care of the core computer equipment up to the panel, and we work with the Honeywell technicians to maintain the end devices. They also provide training to our system operators as needed. Our maintenance and operations departments have really benefited from the service relationship.”
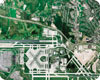
SYSTEMS INTEGRATION
With heightened security concerns following 9/11, PIT officials wanted the ability to monitor and control all building systems from its Emergency Operations Center (EOC). The vision was that EOC operators would not only control HVAC and lighting systems through a centralized management platform, but also life safety, security other building systems to provide the most safe and comfortable environment for travelers and airport personnel.It was recommended that the airport migrate to Honeywell’s Enterprise Buildings Integrator (EBI), an enterprise management system that boosts efficiency and reduces operating costs by integrating core building technology, and allowing operators to view and control these functions from a single workstation. With EBI, PIT would be able to tie nearly all building systems into a flexible, open architecture while keeping its existing control equipment in place. After extensive planning, the installation was complete in 2002 with no system downtime.
The EBI system, consisting of two redundant servers and 11 stations, was customized to the airport’s specifications, largely mirroring the look and feel of the old interface. This minimized the workflow learning curve for operators, allowing them to instantly understand the data presented to them and reduce training time.
“The EBI transition was incredibly smooth,” Long said. “We never lost our screens or control of any system, thanks to careful planning. Our IT people also love it because it has the ability to integrate without adding other systems.”
A TRUE TEST
The most outstanding demonstration of the power of EBI, according to Long, came during a smoke test conducted by PIT and its fire department not long after technicians installed the system. Airport officials wanted to verify how smoke would travel throughout a particular area of the terminal in the event of a fire. To test smoke control capabilities — involving the combined use of fire alarm and HVAC systems — the fire department set up artificial smoke machines to simulate a blaze in one of the retail stores located along the concourse. When the test was run and the alarm system detected smoke, the HVAC system immediately kicked in, ventilating the area exactly as planned.“It was amazing, there was literally a wall of smoke on one side and clear air on the other,” said Long. “The whole integrated system worked extremely well and gave us great confidence that it was finely tuned.”
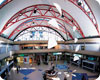
OTHER SYSTEMS ARE INTEGRATED
In addition to HVAC, fire and security, PIT has integrated other systems onto EBI, including a defibrillator system. If someone in the airport has a heart attack or other medical emergency and a defibrillator unit is taken from its location, EOC operators are automatically notified through an alarm, telling them the exact location of the incident and helping emergency responders take action as quickly and effectively as possible.PIT also has linked its fire system into all off-site buildings, including hangars, fuel farms, maintenance garages, parking garages and rental car buildings, and is exploring ways to tie in data from its security video system, as well as the airport’s Flight Information Display System (FIDS), the network of screens across the airport detailing flight arrival and departure times.
“What we want is complete control of our building operations from one centralized location,” Long said. “Linking FIDS into EBI is just another step in that evolution. It will allow us to make changes to the screens across the terminal from the EOC, something we couldn’t do before.”
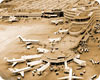
ENERGY CONSERVATION
With the reduced number of flights and travelers after 9/11, as well as the continual rise in fuel costs, the airport also recognized the need to gain better control of its energy use across its facilities to help offset these pressures. In response, PIT established an energy management team made up of airport management, facilities personnel and consultants who meet on a monthly basis to assess energy conservation opportunities throughout the airport.“Taking a proactive approach in identifying energy saving opportunities, as well as ways to better utilize our systems through EBI, has allowed the airport to realize improvements in the bottom line each year,” Long said.
For example, the rooftop units that heat and cool the airport have been optimized to minimize electrical consumption, escalators and moving walkways are shut down at night when traffic is relatively low, and occupancy sensors have been placed throughout areas of the terminal to minimize lighting use, particularly at night. With guidance, PIT also is exploring submetering across the terminal to better understand and regulate energy use with tenant organizations, such as retail outlets.
SKY'S THE LIMIT
PIT looks to expand its capabilities beyond the airport and tie in building systems at the nearby Allegheny County Airport, both managed by the airport authority.“Each year, my staff comes up with some great ideas for how to improve our operations and systems,” Long said. “And Honeywell helps provide the technology and expertise to implement those ideas and keep us moving forward.”
SIDEBAR: Pittsburgh International Airport Major Expansion Timeline
1952 – The airport’s original terminal is built, and is considered to be one of the most modern and spacious in the country when it first came online, second only in size to in
1972 – The International Wing is added.
Early 1980s – Several new docks and rotundas are added to increase the number of gates.
Late 1980s – The Allegheny County Airport Authority recognizes the need to expand and update its facilities to accommodate the growing number of domestic and international flights at PIT. “We needed a larger terminal with modern jet ways not only for the growing number of flights, but also for the larger aircraft passing through the airport,” said Tom Long, director of maintenance and a 38-year PIT employee. “We also knew the original facility contained asbestos, as well as old building control equipment that were not able to be upgraded.”
1990 – Construction on the new begins, designed to offer 7.7 million square feet of air-side space, more than 100 gates and a mall of more than 100 restaurants and specialty shops.
1992 – The New Terminal opens to the flying public; Honeywell technology helps control more than 17,000 HVAC points and 9,000 fire alarm points throughout the facility.
1997 – Honeywell upgrades the frontend to its Excel Building Supervisor-Integrated (XBSi), which allowed the airport to migrate to the Microsoft Windows 98 platform from Windows 3.1.
1998 – Honeywell completes a fire alarm expansion, bringing all the remote buildings at PIT onto the fire protection platform.
2002 – PIT completes migration to Honeywell’s Enterprise Buildings Integrator (EBI), an enterprise management system that boosts efficiency and reduces operating costs by integrating core building technology, and allowing operators to view and control these functions from a single workstation.
Looking for a reprint of this article?
From high-res PDFs to custom plaques, order your copy today!