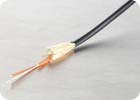
FIGURE
1 A: Cable Suited for Security Applications
Books, white papers and Internet sites are available everywhere to provide guidance on transmission medium for video cameras and other security applications. The format from one to the next is very similar, typically comparing and contrasting the merits of coaxial cable based systems and the various grades of copper unshielded twisted pair (UTP) cables. Their guidance is loaded with an abundance of informative, technical data covering performance characteristics for each.
The topic of optical fiber generally comes right at the end of the segment, and typically goes like this: “Oh yeah, we almost forgot to mention optical fiber. It goes way further, has much better bandwidth capability and far superior signal immunity, is completely non-conductive, is much more difficult to tap, and generally works much better, but it’s hard to terminate and is too expensive. Use it only when you need to go really, really far.” That sentence is usually the end of the paragraph, the end of the chapter and the end of any further mention of optical fiber.
Two myths are still active in the industry, even among experienced professionals:
Myth One– Fiber is extremely difficult to install, terminate and test.
Myth Two– A fiber solution is too expensive.
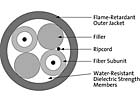
FIGURE
1 B: An Inside Look at the Cable
CONTRARY TO POPULAR BELIEF
In actuality, fiber has become increasingly easy to install, and the cost of complete fiber systems have decreased, while the price of competitive technologies continues to increase. Couple this with the advantages of optical fiber, and the outcome is a solution ideally suited for many needs. Disregarding this new reality may mean unnecessarily sacrificing picture quality or data integrity and increasing long-term security system cost.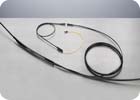
FIGURE
2 A: Plug-and-Play Outside Plant System
Myth One – Optical Fiber is Difficult to Install, Terminate and Test
When one thinks of fiber optic cable, there may be visions, maybe even nightmares, of goopy, messy, flooded cables with fragile, hair-sized, needle-like strands of sharp glass. Terminating those sticky strands once included the painstaking process of meticulously cleaning the fibers to install a fan-out kit, followed by mixing and curing epoxies. The installer could eventually graduate to hours of mindless figure-eight patterns during the connector polishing process.Finally, after all the hard work was complete and the suspense was at its pinnacle, the visual inspection occurred, uneventfully – “Time to polish just a little more!” Those not brave enough to attempt this practice hired a “fiber specialist” or a “fiber guy.” The “fiber guy” was a true craftsman and specialist who had prospered and achieved an elevated status in the structured cabling installation world due to cultivating this unique skill.
The fragile perception of optical cables is that it has physical characteristics that positively impact the initial ease of installation, and has been designed to withstand the demands of even the most cable unfriendly environments.
Fiber optic cables have been the backbone of telephony infrastructures for years, and they normally provide the building-to-building connectivity in campus environments. More and more tactical communications are being handled over fiber optic cables, which have a proven record of success in even the most physically harsh environments. This history of physical and mechanical performance over the years has rendered this part of the myth false.
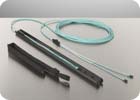
FIGURE
2 B: Standard Plug-and-Play System for Inside Plant Applications
The Evolution of the Optical Cable
The flooded cable previously mentioned was in reference to the longtime use of water blocking gels in outside plant cables. Outdoor cables were most frequently designed with buffer tubes that contained 250-micron fibers surrounded by gel. Cleaning the gel and subsequently installing a fan-out kit were standard practice.New cable designs have eliminated this practice by eliminating gels and replacing them with water-soluble tapes, yarns and powders, ultimately creating “dry” cables. Optical cable manufacturers have also introduced truly dry water blocked cables with 900-micron fibers, which eliminate the need for the fan-out kits altogether on specific outside plant cable designs.
Figure one illustrates a current cable design ideally suited for security applications. This cable design combines the performance of an outdoor cable with the ease of indoor cable installation. The cable can be terminated directly at a camera or in an enclosure with minimal hardware required for protection. The common recommendation is to run a two-fiber cable, although most current transmission equipment literature recommends only one. Additional fibers easily and cost effectively provide room for growth, and also include a spare in case of damage and allow a migration path for future analog to digital Ethernet media conversion
Optical Connectors
Optical connectors have changed, benefiting both the installer and end user. Terminating fiber optic connectors once was slow and laborious, requiring patience, elaborate tools and workspaces. But now, with the use of no-epoxy, no-polish (NENP) connectors have minimized requirements. NENP connectors can generally be installed in less than a minute, and complete training is easily achievable in 30 minutes. Furthermore, the guaranteed end face geometry minimizes finished quality variance. This ensures high-quality insertion loss as well as guaranteed reflectance and results in a better connection. This should be music to the ears of end users and professionals counting on a quick installation with impeccable signal transmission.Fiber optic cable and connectivity manufacturers have also developed completely pre-installed solutions that simply require pulling the cable through and plugging in the hardware. These solutions range from basic drop cable assemblies, which are common in point-to-point applications, to completely engineered campus network solutions. They include high fiber count trunk cables with designated optical drops all built directly into the cable. These are only two of the many options of preterminated assembly concepts engineered to meet a wide range of applications and environments.
Testing and Troubleshooting
Testing and troubleshooting usually represent the final phase of an installation. They also represent the final phase of myth one’s analysis. Fiber testing, like connector terminations, has become increasingly easy to perform. The simple power meter and source throughput test is still the foundation and singular requirement for testing optical links regardless of fiber type and network speeds. The optical time domain reflectometer (OTDR), once an expensive, complicated piece of machinery, is now available with a myriad of price points and feature sets. It has also become extremely easy to use. This stands in contrast to the testing and troubleshooting requirements associated with any UTP or coaxial cables. Testing these cables continues to become more complex as the possibility of signal disruption grows.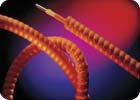
FIGURE
3 A: Interlocking Armored Cable for Crush Resistance and Cable Protection
Myth Two – A Fiber-Based System is Too Expensive
There are simply too many unique variables in play to make definitive blanket statements regarding the cost of one solution over another. Therefore, when attempting to dispel this myth, simply acquire information and a framework for comparison so that the end user, integrator or design engineer can compare processes instead of being intimidated by an old myth.When comparing and contrasting the relative costs of any cabling infrastructure solution, evaluate the processes from many different aspects. Common practice is to let the price of the individual components determine the outcome, but this method may not determine what solution has the greatest long-term value. An effective framework for comparison is to base decisions on comprehensive criteria, including total installed system cost, life cycle cost and management or maintenance costs.
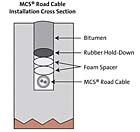
FIGURE
3 B: Schematic of Cable Designed for Quick Installation into Road/Pavement
Total Installed Cost
This concept is simple to grasp, yet difficult to execute. Lack of time, training and critical information can contribute to overlooking this framework. Difficulty aside, an attempt to understand this cost is beneficial. Understanding the implications of all product decisions on installation time and degree of difficulty is the key to understanding total installed cost. There are a large number of items that reduce the total installation cost. The use of optical cable, especially on shorter runs, is thought to be more expensive, but this is not always the case. When fiber is a more expensive alternative, the disparity is often not as great.Optical cabling can reduce total installation cost. The number of multiplexing options makes consolidating cable runs a major cost saver. Utilizing preterminated solutions that reduce labor time vs. field installation is another significant cost reduction. Often, existing dark fiber can be utilized inexpensively. Unique application-specific optical cables can be utilized to reduce cost (a road cable across a parking structure, an interlocking armored cable when no conduit is available, etc.).
About the Source
Security Magazine thanks Sean Kelly of Corning Cabling Solutions for this informative information. Look for an upcoming article highlighting optical fiber costs or visit www.securitymagazine.com for more information on transmission methods.